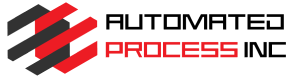
Robotic automation isn’t limited to high-volume part manufacturers. Thanks to recent technological advancements, even companies producing small batches of diverse parts can benefit from automation. Modern automation cells are more affordable than expected and, in many cases, can provide a return on investment in as little as six months.
By implementing an automated system, you can stay competitive by reducing manufacturing costs, boosting throughput, and enhancing product quality. Automation operates two to five times faster than traditional methods, significantly increasing productivity and efficiency. Robots excel at handling repetitive, tedious tasks, allowing skilled workers to focus on more complex processes that are not suitable or cost-effective for automation.
At Automated Process, we are an authorized Fanuc Integration Partner and a proud member of the A3 Association for Advancing Automation. We specialize in providing robotics systems across various sectors. In addition to Fanuc, we offer a range of other robotic brands. Our turn-key systems incorporate the latest technology, safety features, and reliability. Our team of trained professionals supports our customers every step of the way, from initial concept to final installation. Keep reading to explore the wide array of possibilities and applications that today’s advanced robotics can offer.
Robotic dispensing of adhesives, sealers, grease, and other materials delivers superior production efficiency and precision over conventional methods. When integrated with the right dispensing system, robots improve product quality while reducing material waste and scrap. Often, a single robot can manage multiple parts and product configurations within the same work cell. Enhanced by conveyors, shuttles, or turntables, operators can load new parts while the robot continues processing those already in the system. This streamlined approach greatly accelerates manufacturing rates, far exceeding the performance of manual systems.
A Pick and Place robot is a reliable, cost-effective solution that consistently delivers high performance without fatigue. These fast, repetitive robots can outperform both other forms of automation and manual operators. When paired with interchangeable tooling and fixturing, they offer exceptional flexibility. Whether transporting parts to and from equipment or integrated with conveyors, shuttles, turntables, or other automation systems, Pick and Place robots provide a seamless solution for your production needs. They are also ideal for working in dangerous or hazardous environments, removing the risk to personnel and preventing workplace injuries.
Robotic spot welding can be performed in two main ways: by either bringing the part to the welder or by mounting the welding torch directly on the robot. Each method has its unique advantages, with the best choice depending on the specific application. In either case, robotic spot welding offers unparalleled speed and consistency, which manual labor cannot match. Similar to other robotic processes, the use of a shuttle or index table allows operators to load parts while the robot continues welding, eliminating idle time and ensuring continuous operation for both the operator and equipment. This approach significantly enhances efficiency. Besides improving production, robotic spot welding also reduces workplace hazards such as fumes, arc flash, burns, and repetitive motion injuries.
Robotic arc welding provides similar production and safety benefits as robotic spot welding. Robots can be paired with power sources from trusted brands like Miller, Lincoln, OTC-Daihen and others, creating flexible, reliable, and long-lasting welding systems. Automated Process can integrate multiple robots into a single work cell, maximizing floor space and lowering handling costs. Our welding robots are highly adaptable and can be paired with various fixture configurations, material handling modules, and conveyor systems to meet your specific needs.
Robotic packaging and palletizing can be the solution to the repetitive and physically demanding task of handling finished products. When paired with a vision system or an advanced array program, a well-implemented robot can perform high-production, repeatable tasks, while minimizing product damage and reducing work-related injuries. Whether dealing with small, delicate components or heavy bulk materials, our robots are fully equipped to handle the job efficiently and effectively.
How much time is wasted when an operator is required to wait for a production machine to finish its cycle? A machine-tending robot eliminates downtime, allowing your workforce to focus on more critical tasks. This automation also protects your personnel from the risks associated with working around rotating and moving machinery. A robot can be programmed and equipped to load and unload within the same motion cycle. In addition, the robot can present finished parts for automatic gauging or vision inspections if needed. In some cases, a single robot can tend to multiple machines simultaneously, leading to significant improvements in efficiency and production.
Robotic assembly provides a cost-effective solution to replace repetitive manual tasks. By integrating an assembly robot, you can increase profits through improved repeatability, efficiency, and quality. No more missed parts or improper fits. The robot can be equipped with vision systems and advanced sensors for in-process inspections, ensuring that only products that meet your customer’s exact requirements are shipped. Like all robots, these systems work around the clock without issue, ensuring continuous productivity and consistently high-quality results.
Are you excited about innovation and technology? Join our team of experts and partner with a company that is driving the future of industrial automation and robotics.
*By completing this form you're signing up to receive our emails and can unsubscribe at any time